The Science Behind Porosity: A Comprehensive Guide for Welders and Fabricators
Understanding the elaborate systems behind porosity in welding is important for welders and fabricators aiming for remarkable workmanship. From the structure of the base products to the details of the welding process itself, a plethora of variables conspire to either worsen or alleviate the visibility of porosity.
Understanding Porosity in Welding
FIRST SENTENCE:
Exam of porosity in welding exposes critical insights into the stability and quality of the weld joint. Porosity, characterized by the presence of dental caries or spaces within the weld metal, is a typical problem in welding processes. These gaps, if not appropriately addressed, can endanger the architectural stability and mechanical properties of the weld, resulting in possible failings in the ended up item.

To identify and evaluate porosity, non-destructive screening techniques such as ultrasonic screening or X-ray examination are commonly utilized. These techniques allow for the recognition of inner problems without jeopardizing the stability of the weld. By assessing the size, form, and distribution of porosity within a weld, welders can make enlightened choices to enhance their welding procedures and achieve sounder weld joints.

Variables Affecting Porosity Formation
The incident of porosity in welding is affected by a myriad of elements, varying from gas shielding efficiency to the complexities of welding parameter settings. Welding criteria, consisting of voltage, current, travel rate, and electrode type, additionally effect porosity development. The welding strategy employed, such as gas metal arc welding (GMAW) or secured steel arc welding (SMAW), can influence porosity development due to variations in heat distribution and gas insurance coverage - What is Porosity.
Effects of Porosity on Weld High Quality
Porosity development considerably endangers the structural honesty and mechanical residential or commercial properties of bonded joints. When porosity exists in a weld, it creates spaces or dental caries within the product, decreasing the general toughness of the joint. These gaps act as anxiety focus factors, making the weld much more at risk to splitting and failing under lots. The presence of porosity also you could check here compromises the weld's resistance to rust, as the trapped air or gases within deep spaces can respond with the surrounding setting, resulting in deterioration gradually. In addition, porosity can prevent the weld's ability to endure stress or influence, further jeopardizing the overall quality and reliability of the welded framework. In crucial applications such as aerospace, vehicle, or structural building and constructions, where safety and toughness are extremely important, the destructive results of porosity on weld top quality can have serious repercussions, highlighting the importance of reducing porosity via appropriate welding strategies and treatments.
Methods to Reduce Porosity
Furthermore, making use of the appropriate welding specifications, visit this site right here such as the right voltage, existing, and take a trip rate, is crucial in preventing porosity. Preserving a constant arc size and angle throughout welding additionally aids minimize the probability of porosity.

Using the ideal welding method, such as back-stepping or employing a weaving activity, can also help disperse warm equally and minimize the chances of porosity formation. By applying these techniques, welders can effectively decrease porosity and create high-quality bonded joints.
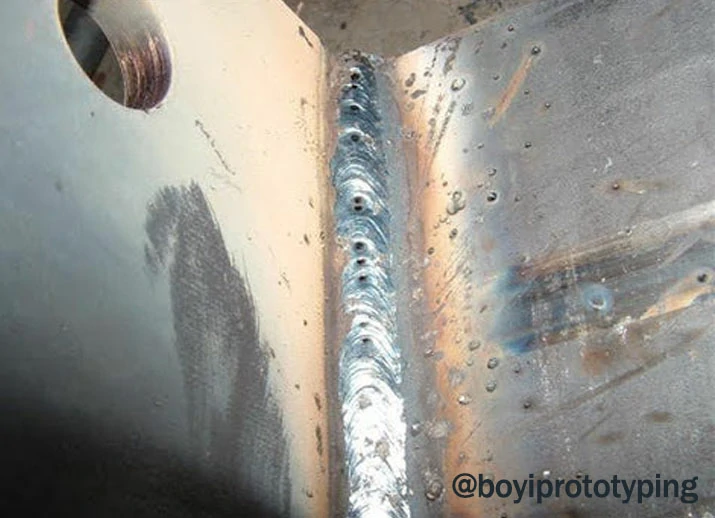
Advanced Solutions for Porosity Control
Executing cutting-edge modern technologies and ingenious methods plays an essential function in accomplishing superior control over porosity in welding processes. One sophisticated remedy is using advanced gas blends. Shielding gases like helium or a combination of argon and hydrogen can help in reducing porosity by giving better arc stability and boosted gas insurance coverage. Additionally, using advanced welding methods such as pulsed MIG welding or modified environment welding can additionally assist mitigate porosity issues.
Another innovative remedy entails the usage of sophisticated welding tools. For example, using tools with integrated features like waveform control and advanced source of power can enhance weld quality and decrease porosity risks. The execution of automated welding systems with accurate control over parameters can considerably reduce porosity problems.
Additionally, including innovative surveillance and examination innovations such as real-time X-ray imaging or automated ultrasonic testing can help in finding porosity early in the welding process, permitting instant restorative actions. Overall, integrating these innovative remedies can considerably boost porosity control and enhance the overall top quality of welded components.
Verdict
In final thought, comprehending the science behind porosity in welding is essential for welders and producers to create high-quality welds. By recognizing the factors affecting porosity development and implementing strategies to lessen it, welders can improve the overall weld top quality. Advanced services for porosity control can additionally enhance the welding procedure and guarantee a solid and reliable weld. It is very important for welders to click to investigate continuously enlighten themselves on porosity and execute finest techniques to accomplish optimum results.